Additive Manufacturing of Pharmaceutical Dosage Forms Containing Mesoporous Materials
Utilizes the additive manufacturing technique Fused Deposition Modeling (FDM) to produce novel, tailor-made oral dosage forms containing drug-loaded mesoporous materials.
About the project
This project is utilizes the additive manufacturing technique Fused Deposition Modeling (FDM) to produce novel, tailor-made oral dosage forms containing drug-loaded mesoporous materials. Oral dosage forms for drug delivery are commonly produced using tableting machines that can produce thousands of tablets in short periods of time, but in certain situations there are the requirements for specific drug loadings or dosage forms, for example in pediatrics. 3D printing techniques such as FDM offer the clinician the ability to rapidly produce specialized dosage forms on demand. With FDM, a filament comprised of the drug, a thermoplastic polymer and perhaps other excipients, is loaded into the FDM printer, see Figure 1. Different tablet sizes, geometries and infill patterns can be printed to produce a desired drug release behavior. Moreover, different tablet shapes and colors can be used to improve patient compliance, which can be beneficial within pediatric care.
A large proportion of newly developed drugs are poorly soluble in aqueous media, which presents a challenging problem in oral dosage form design since a drug that doesn’t sufficiently dissolve when taken orally may not reach the patient’s bloodstream in high enough concentrations to be therapeutically effective. It has been shown that incorporating poorly soluble drugs within the pores of mesoporous materials (i.e., materials with pores in the size range 2-50 nm) can prevent the drug from crystallizing, and consequently results in a higher apparent solubility and faster drug release compared to the crystalline form of the drug. In this project we incorporate drug loaded mesoporous materials within a filament that is subsequently printed into oral dosage forms using the FDM technique.
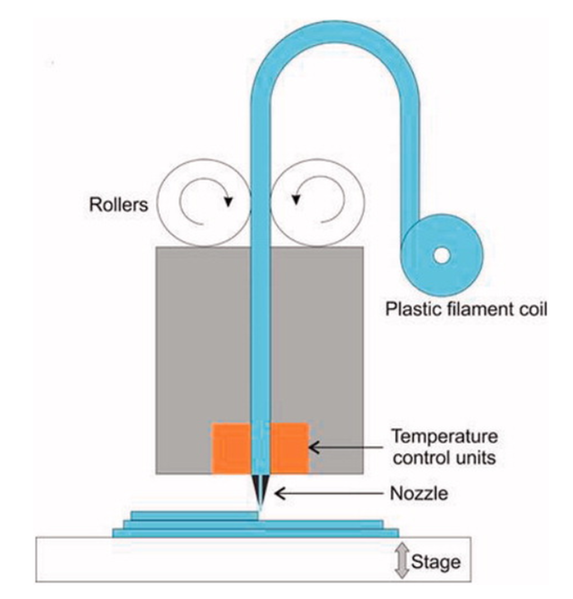
Schematic of a Fused Deposition Modeling (FDM) printer (left panel). A filament that contains, among other materials, a dissolvable thermoplastic is fed into the printer head, which warms the filament and softens it to the point that it can be extruded through the printing nozzle. The printed object is printed layer by layer, where either the stage or printing head is moved after each layer is complete.

Example of a FDM printed oral dosage form with an infill pattern that enhances dissolution by exposing more surface area to the dissolving media.